Ingenious Methods to Fillet Weld Assessment and Screening: Enhancing Weld Quality and Compliance Requirements
In the realm of welding, the high quality and stability of fillet welds play a crucial role in guaranteeing the architectural soundness and reliability of numerous industrial components. With the continuous drive for boosted effectiveness and compliance with strict criteria, the expedition of cutting-edge strategies to fillet weld inspection and screening has ended up being vital. As industries evolve, the conventional approaches may no more be adequate in meeting the demands of contemporary welding applications (Gauge Fillet Weld). By accepting sophisticated modern technologies and techniques, a new perspective of possibilities emerges in the realm of weld top quality evaluation and adherence to compliance standards.
Advanced Non-Destructive Testing Techniques
Using modern innovations, progressed non-destructive screening methods play a crucial role in making certain the stability and quality of fillet welds. These methods, such as phased array ultrasonic screening (PAUT) and magnetic particle screening (MPT), deal detailed understandings into the weld's internal framework without creating any kind of damages to the product. PAUT, as an example, utilizes numerous ultrasonic components to inspect the weld from numerous angles, giving a detailed visualization of possible flaws like absence of blend or cracks.
By utilizing these advanced non-destructive testing methods, weld inspectors can accurately analyze the high quality of fillet welds, making sure compliance with market criteria and laws. The capacity to detect problems early on not only enhances weld top quality however also stops expensive rework or failings in structural integrity, underscoring the importance of these innovative testing techniques in welding examinations.
Robotics and Automation in Evaluation

The assimilation of robotics and automation has changed the evaluation process for fillet welds, enhancing effectiveness and precision in high quality assessment. Robotics offer specific control and repeatability in evaluating welds, making certain regular and trusted outcomes. Automated systems can be set to comply with specific inspection courses, guaranteeing thorough protection of welds and decreasing the risk of human mistake.
Robotic assessment systems equipped with sophisticated sensing units can detect and gauge weld functions with high precision, supplying thorough information for evaluation. These systems can recognize problems such as cracks, absence of combination, and porosity, enabling prompt rehabilitative actions to be taken. In addition, robotics and automation enable real-time data collection and evaluation, giving prompt comments to operators and facilitating quick decision-making processes.
Furthermore, the usage of robotics and automation in fillet weld evaluation boosts total productivity by minimizing evaluation times and increasing inspection throughput. By simplifying the assessment procedure, makers can ensure weld top quality and compliance criteria are satisfied effectively, inevitably bring about cost financial savings and enhanced item high quality.
Making Use Of Artificial Intelligence for Evaluation
Fabricated knowledge plays an essential duty in improving the efficiency and precision of analysis in fillet weld examination processes. By utilizing the power of AI, examiners can streamline the analysis of weld high quality and compliance criteria, leading to extra trusted and accurate results. AI formulas can quickly refine huge amounts of data from weld examinations, detecting flaws or disparities that might be challenging to relate to the naked eye. This innovative innovation makes it possible for real-time monitoring of weld high quality, enabling immediate rehabilitative activities to be taken if any type of concerns are discovered.
Moreover, AI systems can gain from past examination information, continually boosting their capacity to determine potential problems and inconsistencies in fillet welds. This flexible learning capacity improves the overall quality assurance process, lowering the probability of human error and making sure that welds satisfy the needed requirements. By incorporating expert system into fillet weld evaluation, markets can accomplish higher levels of efficiency, uniformity, and conformity in their assessment techniques.
Portable Equipment for On-Site Evaluation
Enhancing area examination effectiveness, the adoption of mobile tools reinvents on-site assessment procedures for fillet welds. These tools provide adaptability and ease, permitting inspectors to perform extensive examinations in various places, including remote or difficult atmospheres. Portable tools such as ultrasonic testing tools, magnetic particle inspection equipment, and digital radiography systems give real-time data and high-resolution imaging capabilities, enabling fast decision-making and prompt comments on weld top quality.
One substantial advantage of mobile devices is their ability to enhance inspection procedures, decreasing downtime and enhancing total efficiency - Gauge Fillet Weld. Inspectors can quickly transport these tools to different task sites, eliminating the need for delivering heavy equipment or components to off-site centers. In addition, the transportability of these tools promotes cost-effectiveness by lessening transport costs and increasing assessment timelines
Moreover, making use of mobile tools for on-site assessment promotes aggressive quality assurance procedures, as examiners can without delay recognize and address any kind of potential welding problems or discrepancies. By including these cutting-edge modern technologies right into on-site assessment methods, welding experts can make sure conformity with industry requirements and enhance weld quality, eventually leading to boosted structural stability and safety and security in numerous welding applications.
Assimilation of Data Administration Solution
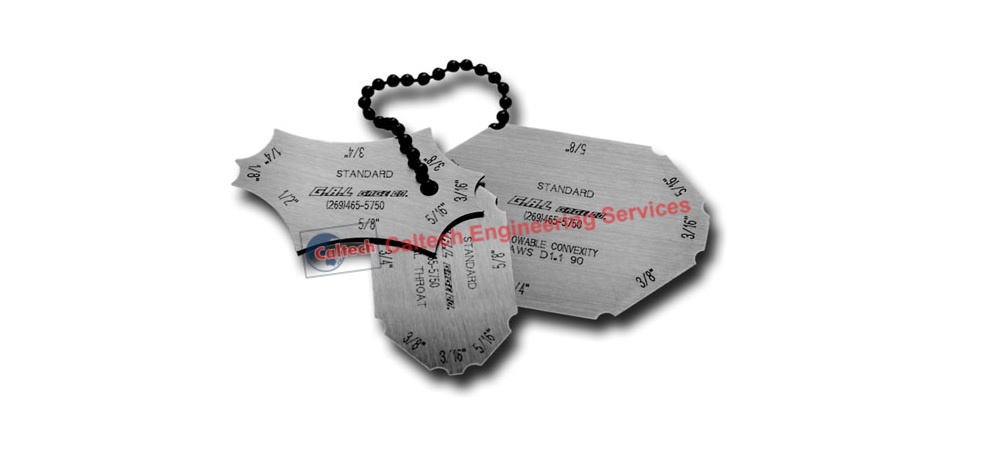
Having maximized on-site assessment procedures through the utilization of mobile tools, the next phase involves the smooth assimilation of data management systems to additionally boost efficiency and data analysis capacities in fillet weld assessment and screening. By incorporating data monitoring systems into the evaluation procedure, organizations can enhance information collection, storage, and evaluation. This assimilation allows for real-time tracking of weld quality, instant identification of flaws, and prompt decision-making to rectify any issues that may develop during the assessment procedure.
The combination of information administration systems makes it possible for smooth communication in between various stakeholders entailed in the assessment process, promoting cooperation and improving general quality control steps. Inevitably, the combination of data monitoring systems serves to elevate the standards of fillet read the article weld inspection and click this link testing, ensuring conformity with sector guidelines and boosting weld top quality.
Verdict
Finally, cutting-edge approaches to fillet weld evaluation and testing have dramatically improved weld high quality and conformity standards. Advanced non-destructive testing techniques, robotics, automation, man-made knowledge, portable devices, and information monitoring systems have actually reinvented the method weld assessments are performed. By making use of these technologies, markets can make certain that welds meet the required quality standards and laws, eventually boosting general performance and security in welding procedures.

Having maximized on-site evaluation processes with the use of portable devices, the following phase involves the smooth combination of information management systems to better enhance efficiency and information analysis abilities in fillet weld assessment and screening. Eventually, the integration of data administration systems serves to elevate the criteria of fillet weld examination and testing, making certain compliance with sector policies and improving weld quality.
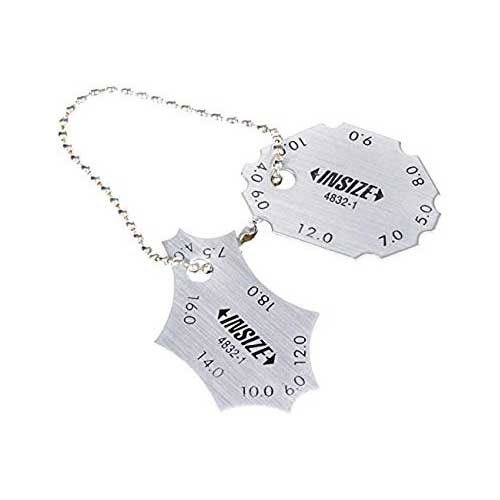